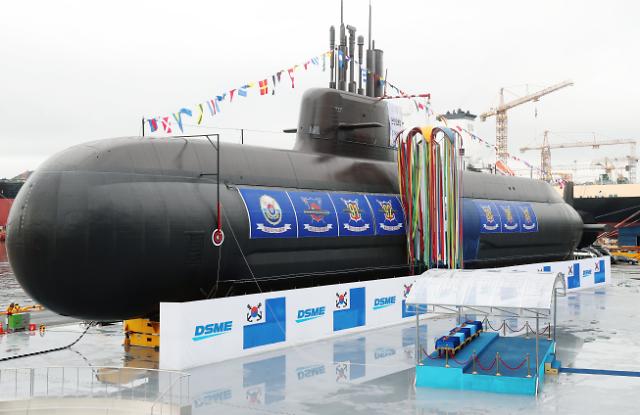
[Yonhap Photo]
DSME said that researchers from the shipbuilder, Posco and Korean Register (KR) would join forces to acquire elevated technology for pressure hull design by 2021 under an agreement on joint research and development. KR is a classification society offering verification and certification services for ships. Posco, a steel giant in South Korea, will provide high yield special steel for submarines.
"As this joint research project is aimed at securing fatigue design technology, which is directly related to the survival of submarines, it will play a major role in securing capabilities for domestic submarines and export models in the future," said Yoon In-sang in charge of DSME's special ship design. it is important to avoid fatigue in welds and fatigue design technology determines the survival of submarines.
A submarine hull has two major components. The outer non-watertight hull provides a hydrodynamically efficient shape while the inner pressure hull maintains structural integrity. The pressure hull, which withstands the outside pressure, is constructed of thick high-strength steel with a complex structure and high strength reserve.
South Korea has a three-stage project to develop a fleet of submarines. Through the first phase, nine 1,200-ton diesel-electric submarines have been built with technical help from Germany’s Howaldtswerke-Deutsche Werft (HDW). The second phase calls for the construction of six 1,800-ton vessels. Through the third phase, submarines of 3,000 tons or more are to be built with indigenous technologies. The first 3,000-ton submarine, unveiled in September last year, can sail at a maximum speed of 37 kilometers per hour with about 50 people aboard.
Copyright ⓒ Aju Press All rights reserved.